The industrial landscape is undergoing a transformation. Driven by technological advancements and the ever-increasing demand for efficiency, automation is rapidly evolving. Factory floors are no longer solely populated by hulking machines; they’re becoming intelligent ecosystems where physical processes seamlessly integrate with the digital world.
This blog explores ten key trends that are shaping the future of industrial automation control:
1. Industrial Internet of Things (IIoT):
At the heart of this transformation lies the IIoT. Sensors embedded in machines and throughout the production process collect real-time data on everything from machine health to environmental conditions. This data is then transmitted and analyzed, enabling better decision-making, predictive maintenance, and optimized production processes.
2. Artificial Intelligence (AI) and Machine Learning (ML):
The power of AI and ML is revolutionizing industrial automation. By analyzing vast amounts of data collected through IIoT, AI and ML algorithms can identify patterns, predict equipment failures, and optimize processes in real-time. This allows for proactive maintenance, reduced downtime, and improved overall equipment effectiveness (OEE).
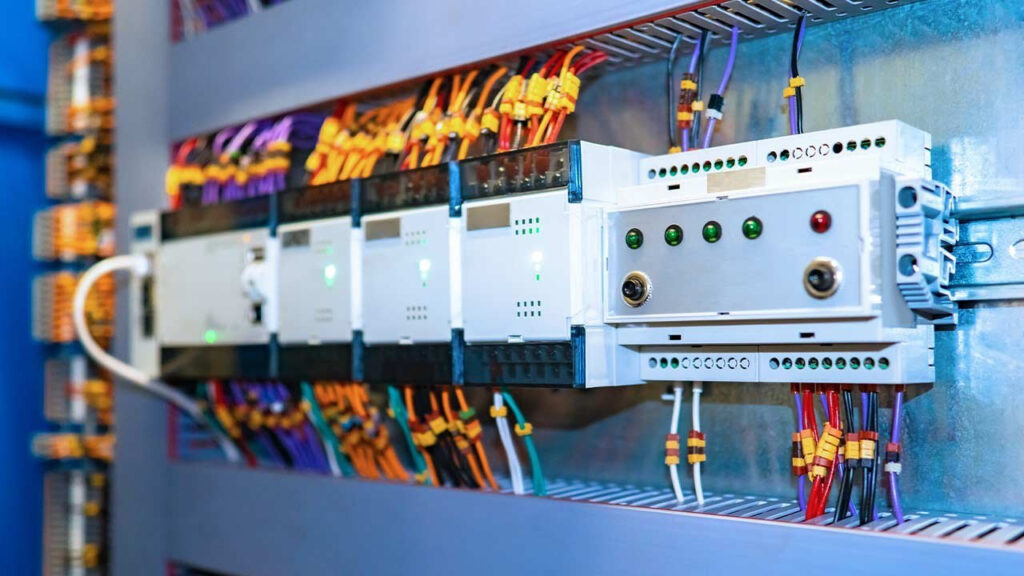
3. Edge Computing and Cloud Integration:
The sheer volume of data generated by IIoT sensors can overwhelm traditional centralized computing systems. Edge computing addresses this by processing critical data at the network’s edge, closer to the source. This reduces latency and enables faster decision-making for time-sensitive processes. However, edge computing often works in conjunction with cloud platforms for data storage, advanced analytics, and historical trend analysis.
4. Collaborative Robotics (Cobots):
The rise of cobots is fostering a paradigm shift in human-robot interaction. Unlike traditional industrial robots, cobots are designed to work safely alongside humans, performing tasks that are repetitive, hazardous, or require high dexterity. This collaborative approach allows humans to focus on higher-level tasks like planning, supervision, and quality control.
5. Digital Twin Technology:
A digital twin is a virtual replica of a physical asset or process. By creating a digital twin of a production line, manufacturers can simulate and optimize processes before implementing them in the real world. This allows for identifying and eliminating potential bottlenecks, testing new configurations, and optimizing production for efficiency and cost savings.
6. Cybersecurity:
As industrial systems become more interconnected, the need for robust cybersecurity measures becomes paramount. With increased reliance on IIoT devices and cloud-based platforms, protecting against cyberattacks that could disrupt operations or compromise sensitive data is crucial. Implementing secure protocols, access control systems, and continuous monitoring are essential for safeguarding industrial automation infrastructure.
7. Advanced Human-Machine Interface (HMI) Systems:
The way humans interact with automated systems is also evolving. Advanced HMI systems provide operators with intuitive interfaces that display real-time data, process visualizations, and augmented reality overlays. This allows for better situational awareness, improved decision-making, and faster troubleshooting of issues.
8. Energy Efficiency:
Sustainability is a growing concern for manufacturers. Industrial automation technologies play a significant role in optimizing energy consumption. By monitoring energy usage throughout the production process, AI and ML algorithms can identify areas for improvement and implement strategies for reducing energy waste. Additionally, advancements in motor control technology and power conversion systems further improve energy efficiency.

9. Blockchain for Supply Chain Management:
Blockchain technology offers a secure and transparent way to track materials and products throughout the supply chain. This can improve traceability, reduce counterfeit incidents, and streamline logistics. In the context of industrial automation, blockchain can be used to ensure the authenticity of components used in production, optimize inventory management, and improve overall supply chain visibility.
10. Wearable Technologies:
Wearable technology is making its way onto the factory floor. Smart glasses, augmented reality headsets, and exoskeletons are being used to improve worker safety, efficiency, and training. Wearables can provide workers with real-time instructions, improve maintenance procedures through remote guidance, and even reduce physical strain through exoskeleton support.
Future of Industrial Automation
These ten trends represent just a glimpse into the exciting future of industrial automation control. As these technologies continue to develop and converge, we can expect to see even more intelligent and interconnected factories emerge, driving increased productivity, improved efficiency, and a more sustainable future for manufacturing.
Conclusion
In conclusion, the industrial automation landscape is undergoing a period of significant transformation. The ten trends explored in this blog highlight the increasing integration of physical and digital systems, the power of data analytics, and the rise of collaborative technologies. By embracing these advancements, manufacturers can unlock a new era of industrial automation, characterized by improved efficiency, optimized processes, and a more sustainable and worker-centric future for factory operations.
Thank you for being such a source of inspiration and encouragement for your readers.
Great Post!